Analysis of Production Process for 26650 Lithium Battery Pack.
This article mainly shares with you the detailed process and precautions of lithium battery pack production technology. Collect it now! In the production process of lithium battery packs, after the production of electrode sheets is completed, the positive and negative electrode sheets and separators are assembled and manufactured into basic battery cells using winding or stacking methods. Subsequently, the battery cells are usually subjected to hot pressing and shaping. Below is a brief introduction to the process and process control points of hot press shaping technology. Open your eyes wide and keep an eye on it.
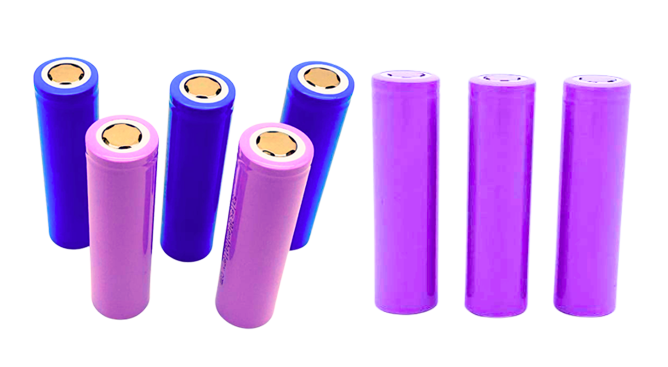
1、 The production process of
lithium battery packs aims to ensure that the lithium-ion battery cells are flat after shaping and avoid shrinkage and recovery. The process of hot pressing and shaping of battery cells is as follows: place the wound or laminated battery cells on a template, set the pressure of the booster cylinder and the temperature of the template, and then use the upper and lower templates to shape the battery cells under certain pressure and temperature to achieve consistent thickness, reduce the elasticity of the battery cells, lower the qualified rate of core assembly, and ensure the consistency of the thickness of the finished battery cells. For square batteries, the hot pressing shaping device is shown in Figure 1. The upper and lower templates are flat plates, and under pressure, the flat plates are pressed together to flatten the battery cells. For cylindrical batteries, the hot pressing shaping device is shown in Figure 2, which consists of two cylinders fixed on the base to generate opposing motion. Two semi-circular molds with cylindrical grooves are located at the end of the piston rods of the two cylinders, and the radii of the cylindrical grooves of the two semi-circular molds are equal to or less than the preset core radius. Using a robotic arm or fixture to hold the core and place it at the center of two semi-circular molds, control the two cylinders to drive the two semi-circular molds to move towards each other, so that the two semi-circular molds can squeeze the core and shape it to the preset size, allowing it to be placed into the matching outer shell. Generally, during the hot pressing process of battery cells, insulation and voltage resistance tests are conducted to detect the presence of micro short circuits inside the cells. If there are tiny metal foreign particles inside the battery cell, it is easy to detect micro short circuit non-conforming products when the battery cell is pressed down and the battery cell diaphragm is pierced.
2、 The main process parameters for hot pressing and shaping of lithium battery packs include pressurization pressure, pressurization time, and template temperature. Under appropriate process parameters, there is almost no air inside the thick battery cell, and the diaphragm and pole pieces are tightly bonded together. Loose battery cells can become hard blocks. In the process determination test, the testing items include the permeability and thickness variation of the diaphragm; Does the thickness of the battery cell meet the requirements for casing; Whether the polarizer has broken, etc. The battery separator, as the core component of a lithium battery pack, plays a crucial role in isolating the conduction of positive and negative electrons while allowing lithium ions to pass back and forth between the two poles. The microporous structure on the separator is an important channel for these ions to travel back and forth between the positive and negative electrodes, and its permeability directly affects the performance of the battery. The permeability of the separator refers to the amount of gas that can pass through it under a certain time and pressure. If the permeability of the separator is poor, it will affect the transfer of lithium ions between the positive and negative electrodes, thereby affecting the charging and discharging of lithium batteries. The testing process involves fixing the battery separator, applying air pressure on one side of the separator, measuring the pressure drop and time used, and testing the permeability of the separator. The shorter the time used, the better the permeability. During the hot pressing process, the diaphragm may be severely compressed and the thickness of the diaphragm may vary greatly, causing the micropores to be blocked. The diaphragm will turn transparent when observed with the naked eye. This situation indicates that the effect of hot pressing on the battery cell exceeds the limit, which will affect the transmission of lithium ions. The wound battery cell is shown in the figure. If the electrode is relatively brittle, the bending of the battery cell during hot pressing is prone to powder loss or even breakage, which can limit electronic transmission and increase the internal resistance of the battery. Therefore, the hot pressing shaping of battery cells must also avoid this situation. These two aspects require that the lower the pressure of hot pressing, the better, and the shorter the time, the better.
3、 Safety issues to be aware of during the production process of lithium batteries: (1) Insufficient understanding of the toxicity of battery fluids, and many companies are unaware that battery fluids are toxic. (2) The optimization of electrolyte composition and the production process of lithium batteries require the electrolyte to maintain capacity and extend battery life. The high bonding strength of electrode coatings is conducive to reducing the rate of decrease in cycling capacity, which is the most technically advanced process in lithium battery production. Therefore, attention should be paid to it Insufficient understanding of the fire and explosion hazards of lithium battery packs. Alright, the above is a detailed explanation of the production process of lithium battery packs and the safety issues to be aware of during the production of lithium battery packs,
Did you remember? do you understand? If not, then quickly save this article and keep it for future reference.