What is the production process of 18650 lithium battery pack?
The production process from a simple battery cell to a lithium-ion battery pack is also quite complex, requiring multiple processes, which is no simpler than the manufacturing process of battery cells.
1. Loading
Transfer the battery cells to the designated location, and the robotic arm automatically grabs and sends them into the mold assembly wiring.
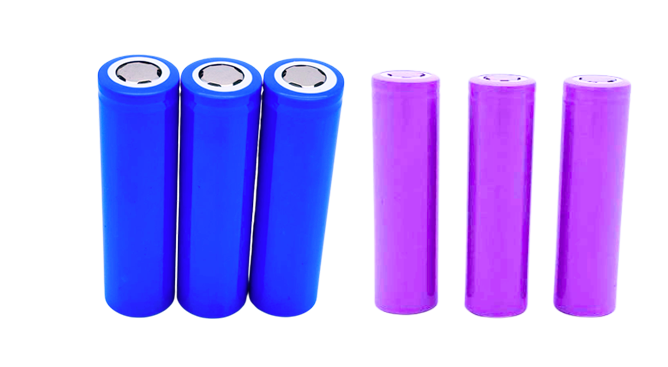
2. Give the battery cell a bath and plasma cleaning process
Clean the surface of each battery cell. Ionic cleaning is used here to ensure that pollutants do not adhere to the bottom of the battery cell during the process. Why use plasma cleaning technology? The reason is that plasma cleaning technology is the most thorough stripping cleaning method among cleaning methods. Its biggest advantage is that there is no waste liquid after cleaning, and its biggest feature is that it can handle metals, semiconductors, oxides, and most polymer materials well, achieving overall, local, and complex structure cleaning.
3. Combine the battery cells and apply adhesive to them
Before assembling the battery cells, the surface should be coated with adhesive. The purpose of adhesive coating is not only for fixed purposes, but also for insulation and heat dissipation. High precision glue coating equipment and robotic arm cooperation can set the trajectory for glue coating, while monitoring the quality of glue coating in real time to ensure the quality of glue coating, further improving the consistency of different battery modules in each group.
4. Build a home end plate and side plate welding for the battery cell
Battery modules are often made by welding aluminum end plates and side plates, which are laminated and welded by robots.
5. Assembly of wire harness isolation board
After the welding monitoring system accurately locates the welding position, it binds the barcode of the wire harness isolation plate material to the MES production scheduling management system and generates a separate code for traceability. After coding, the wire harness isolation board is automatically installed into the module through a robotic arm.
6. Complete the series parallel laser welding of batteries
By automatic laser welding, the connection between the pole and the connecting piece is completed, achieving battery series and parallel connection.
7. An important offline test before going offline
Before going offline, conduct a comprehensive performance check on the module, including module voltage/resistance, battery cell voltage, withstand voltage test, and insulation resistance test. The standardized module design principle can be customized to match different car models, and each module can also be installed in the best suitable space and predetermined position inside the car.