After years of development, the
lithium battery industry has formed a complete industrial chain with a high degree of specialization and division of labor. With the support of national policies and the introduction of new national standards for electric vehicles,
lithium batteries will be the preferred choice for golf carts in the future. So, how are high-quality
lithium batteries made for golf carts?
Step 1: Ingredients
High vacuum fully automatic stirring of materials takes 10 hours to disperse the materials required for lithium batteries evenly, improving the consistency and comprehensive performance of the battery. Why do we have to do this? Because ingredients are the core area of lithium battery production, poor ingredients directly affect the performance of lithium batteries.
Step 2: Coating
Using an automatic feeding system, an automatic knife adjustment system, and an online thickness measurement system, the positive and negative electrodes are evenly coated. Why do we have to do this? Because coating is the foundation of
lithium battery production, coating determines the consistency of the battery.
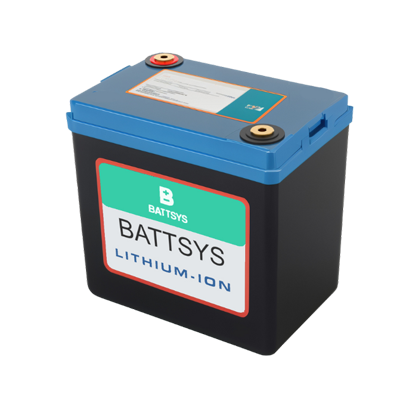
Step 3: Align the rollers
After the positive and negative electrode plates are coated, the positive and negative materials are relatively loose, and a certain pressure needs to be applied to the electrode plates to compact the positive and negative electrode materials to a certain range.
Step 4: Splitting
According to the battery model, the positive and negative electrodes need to be cut into the required width. For example, in 18650 lithium batteries, the electrode width is within 56-58mm.
Step 5: Production and winding
Using a fully automatic film making machine, solder the positive and negative electrode ears onto the positive and negative electrode plates. And a fully automatic winding machine is used to wind the positive and negative electrodes and diaphragm together into a cylindrical shape.
Step 6: Point bottom rolling groove and vacuum drying
Put the core into the steel shell, automatically weld the negative electrode ear, and automatically roll the groove. In addition, through high vacuum and high temperature baking, a small amount of water is dried to ensure the performance of the lithium battery.
Step 7: Dissolve into volume fraction
Lithium batteries need to undergo charging and discharging tests before shipment, and the batteries are in a point state before leaving the factory.
Step 8: Assemble the lithium battery
A fully automatic welding machine is used to weld multiple batteries together with connecting pieces, and then install a circuit board for aging testing and shipment inspection.