Precision production process of 18650 battery.In our Battsys production manufacturer, the detailed steps of the
18650 lithium-ion battery production process are as follows:
The first aspect is electrical grade manufacturing, where the positive and negative electrode materials are mixed before coating to ensure the uniformity of the slurry. Positive electrode materials include active materials such as NMC622, polymer binder PVdF, solvent NMP, and conductive additives (such as carbon), while negative electrode materials include active materials (such as graphite or graphite+silicon), conductive materials (such as carbon black), and polymer binders (such as carboxymethyl cellulose, CMC);
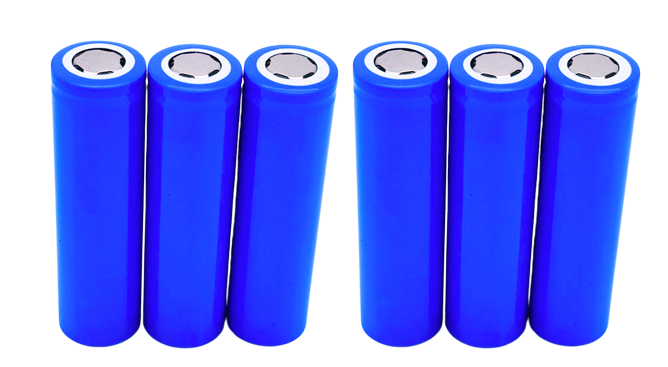
The positive and negative electrodes are covered separately during the continuous coating process. The metal oxide of the lithium-ion battery in the positive electrode is coated on the aluminum electrode, and the polymer binder adheres the positive and negative electrode coatings to the copper and aluminum electrodes, respectively;
The electrode to be coated should be immediately dried using a convection air dryer for continuous drying, during which the solvent will be recovered;
Then roll the electrode to achieve controlled thickness and porosity.
The second aspect is battery assembly, which requires cutting the electrodes to a width that matches the final size of the battery during slitting;
Dry the electrodes again before battery assembly to remove all solvent content and reduce free water ppm;
Next, cut the electrode into its final shape, including labels for the electrode. In cylindrical batteries, the anode and separator are wound in a spiral shape. For soft pack batteries, the battery levels are stacked into: anode, separator, cathode, separator, anode, separator, etc;
Then weld the terminals, connecting the anode to the negative terminal and the cathode to the positive terminal;
Finally, pack or encapsulate the electrodes as rolls or stacked layers into a can or soft package.
The third aspect is battery completion, injecting the dried battery into the electrolyte, creating a partial vacuum in the battery, and delivering a predetermined amount of electrolyte to the battery. Partial vacuum helps with the distribution of electrolyte and wetting of all layers.
The above steps involve precise control of materials, uniform coating of electrodes, uniformity and solvent recovery during the drying process, precise cutting and stacking of electrodes, and precise injection of electrolyte, among other closely related process steps. Each step requires strict quality control to ensure the performance and safety of the battery.