Attention should be paid to the use and assembly of 18650 lithium battery cells.
The so-called polymer lithium battery is a kind of lithium battery with gel shaped electrolyte and soft packaging. It is commonly referred to as a soft pack lithium battery in most markets. This makes lithium battery cells different from ordinary liquid lithium-ion batteries. In the same place, there are some special precautions to be taken regarding possible errors that may occur during the use and assembly of batteries. The following precautions are proposed.
1. Precautions for battery use, including aluminum-plastic composite film protection, top sealing (pole edge sealing), side sealing, pole handle, measures to avoid mechanical impact and short circuit.
1. Aluminum plastic composite film outer packaging protection: mainly to avoid damage from sharp parts. For this reason, the surrounding environment of the battery should be cleaned from time to time, and sharp objects should be prohibited from contacting or colliding with the battery cells. Gloves can be worn when taking them to avoid scratching the surface of the battery cells with hands. nail
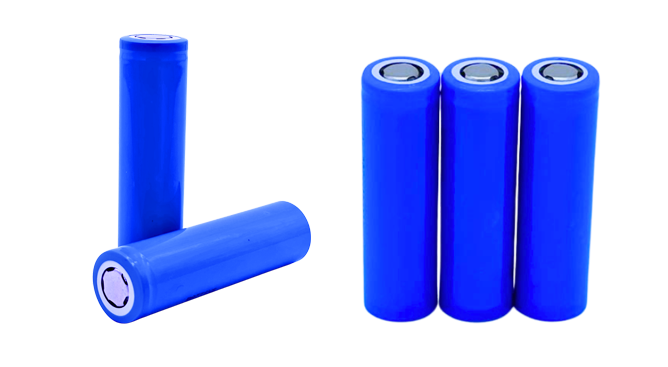
2. Top and edge seal protection: To avoid damage to the top and edge seals and damage to the sealing effect, it is strictly prohibited to bend the top and edge seals; At the same time, reliable insulation isolation measures must be adopted in the design of battery cells to avoid short circuits between the negative electrode and the aluminum-plastic composite film
3. Pole protection: The positive terminal of the polymer lithium battery uses an aluminum pole, and the negative terminal uses a nickel pole. Due to the thin handle, bending should be prohibited; At the same time, during the production process, the handle and aluminum-plastic composite film should be avoided, and the sleeve film should be strictly isolated.
4. Avoid mechanical impacts such as falling, hitting, bending battery cells, and accidentally stepping on batteries.
5. Do not short-circuit the positive and negative poles with metal objects or wires
Two. After a battery cell is completed, the next step is to correctly combine the casing with the battery cell protection circuit module to make it a polymer battery. The precautions during this process are as follows:
1、 Shell design:
(1) Sufficient mechanical strength to avoid mechanical damage to the battery cells caused by external forces;
(2) When installing the battery cell into the casing, avoid scratching the cell with sharp edges and corners of the casing;
(3) Prevent short circuits between pure aluminum in the interlayer of aluminum-plastic composite film and the outside world.
2. It is necessary to design a battery cell protection circuit, including scientific settings for the highest/lowest voltage, overcurrent protection, and overcharge and overdischarge protection for individual battery cells when used in combination.
3. The positive aluminum pole handle is connected to the circuit board through nickel tape, and the connection between the battery cell and the circuit board should be achieved using ultrasonic welding or spot welding technology.
4. The positioning of the battery cells is reliable. After the battery cell is assembled, it should be firmly fixed in the shell and should not be loosened at will, so that the entire lithium battery structure is in a fixed state.
3. Water vapor monitoring in the manufacturing process of lithium batteries
The manufacturing process of producing battery cells is very sensitive to moisture. This challenging production environment requires a reliable and highly tolerant water vapor detector that can detect process by-products that may exist in the air.
2. In the manufacturing process of lithium batteries, the treatment of dry air is extremely important for the following three reasons: firstly, to prevent unnecessary chemical reactions such as fire and explosion; 2、 Eliminate product quality issues; The third is to master and control the cost of drying a large amount of air. At the same time, selecting well-known brand manufacturers ensures long-term stable and efficient after-sales service capabilities, ensuring that the quality of the manufacturer's products is guaranteed to a certain extent.