18650 lithium-ion battery manufacturing process.
1. Baking
Bake for 12 hours under constant temperature and vacuum degree of -0.09MPa, with the important purpose of drying the moisture in the battery cells.
2. Inject liquid
After vacuum baking, the battery cells are injected with electrolyte into a glove box filled with Ar gas. The amount of electrolyte injected varies according to the customized design of the lithium-ion battery pack. The battery must be weighed before and after injection, and the weight difference is the amount of electrolyte injected to determine whether the amount of electrolyte injected is appropriate.
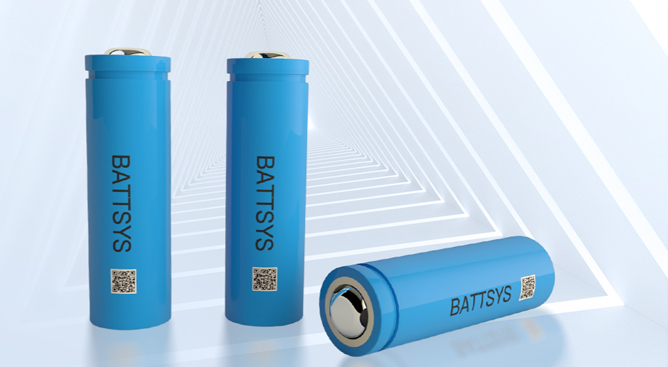
3. Weld the positive electrode ear (aluminum strip) and negative electrode ear (nickel strip) to the scraping positions of the positive and negative electrode plates using an ultrasonic welding machine. Attention should be paid to preventing welding deviation, welding misalignment, and virtual welding.
4. Bottom welding. First, place the insulation gasket into the steel shell, then place the coiled battery cell into the steel shell, and use a spot welding machine to weld the negative electrode ear to the bottom of the steel shell. Inspect the outer surface of the bottom of the steel shell, pick out any appearance defects such as yellow, black, defects, and explosion, and try pulling the electrode ears to pick out customized 18650 lithium-ion battery packs with weak spot welding such as explosion, virtual welding, and desoldering.
5. Sealing
First, use a spot welding machine to spot weld the steel shell and cap of the customized
18650 lithium-ion battery pack, and then continue laser welding with a laser welding machine. Laser welding should ensure accurate positioning, clean the welded area, and strictly prohibit deformation or damage to the battery. After welding, inspection should be carried out to repair defective batteries such as welding holes and explosions.
6. Winding up
Place the ion exchange membrane flat on the winding needle, with the front end extending 2-5mm from the winding needle. There should be no wrinkles at the four corners of the pole piece, and the pole piece should not have defects such as material falling off, tape being slanted, single-sided tape being too long, double-sided tape being misaligned, or tape not covering the welding points. The positive electrode material must hold the negative electrode material, and the pole piece should not be rolled off center. The front end of the pole piece must be inserted to the top.
Previous: Lithium battery prices, electrolyte additives