18650 lithium batteries Manufacturing Process.
(1) Baking
Bake for 12 hours under constant temperature and vacuum degree of -0.09MPa, with the important purpose of drying the moisture in the battery cells.
(2) Inject liquid
Inject electrolyte into a glove box filled with Ar gas after vacuum baking. The amount of electrolyte injected varies according to the battery design, and the battery should be weighed before and after injection. The weight difference is the amount of electrolyte injected to determine whether the amount of electrolyte is appropriate.
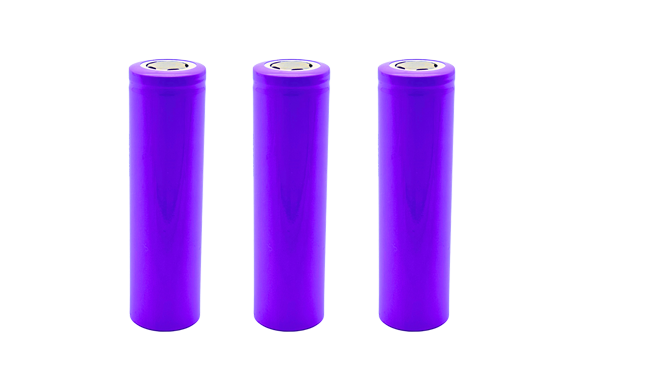
(3) Welding ear
Weld the positive electrode tab (aluminum strip) and negative electrode tab (nickel strip) separately to the scraping positions of the positive and negative electrode plates using an ultrasonic welding machine. Attention should be paid to preventing welding deviation, welding misalignment, and virtual welding.
(4) Bottom welding
First, place the insulation gasket into the steel shell, then place the coiled battery cell into the steel shell, and use a spot welding machine to weld the negative electrode ear to the bottom of the steel shell. Check the outer surface of the bottom of the steel shell, pick out any appearance defects such as yellow, black, defects, and explosion, and try pulling the electrode ears to pick out batteries that cannot be spot welded firmly, such as explosion, virtual welding, and detachment.
(5) Sealing
First, use a spot welding machine to spot weld the steel shell and cap of the battery, and then continue laser welding with a laser welding machine. Laser welding should ensure accurate positioning, clean the welded area, and strictly prohibit deformation or damage to the battery. After welding, inspection should be carried out to repair defective batteries such as welding holes and explosions.
(6) Winding up
Place the ion exchange membrane flat on the winding needle, with the front end extending 2-5mm from the winding needle. There should be no wrinkles at the four corners of the pole piece, and the pole piece should not have defects such as material falling off, tape being slanted, single-sided tape being too long, double-sided tape being misaligned, or tape not covering the welding points. The positive electrode material must hold the negative electrode material, and the pole piece should not be rolled off center. The front end of the pole piece must be inserted to the top.
Check for winding defects: uneven ion exchange membrane, with positive and negative electrodes exceeding the exchange membrane; High slice, low slice; The pole piece is not placed in place, and the positive end of the outer ring is not wrapped around the negative end. In addition, the positive and negative pole pieces of the inner ring are not aligned with the top of the exchange membrane, leaving a distance; The negative electrode tail of the exchange membrane is too tight; The positive aluminum strip and negative nickel strip are too long and too short; Poor adhesive tape at the end of the battery cell; The battery cell is not rolled in place: the distance between the positive and negative electrode ears is too wide or narrow; The exchange membrane is not flattened and wrinkled; Positive electrode edge curling; The positive electrode sheet is not curled or has missing corners; The exchange membrane has not fully wrapped around the tail of the negative electrode; Misalignment of inner and outer polar plates.