18650 battery production and manufacturing process.
The production process of lithium batteries is divided into three major sections: electrode sheet production, battery cell production, and battery assembly. In the production process of lithium batteries, the production of electrode plates is the foundation, the production of battery cells is the core, and battery assembly is related to the quality of lithium battery products. The specific steps in the production process of lithium batteries include positive electrode drawing, negative electrode drawing, positive electrode sheet, negative electrode sheet, steel shell assembly, liquid injection and testing, and packaging.
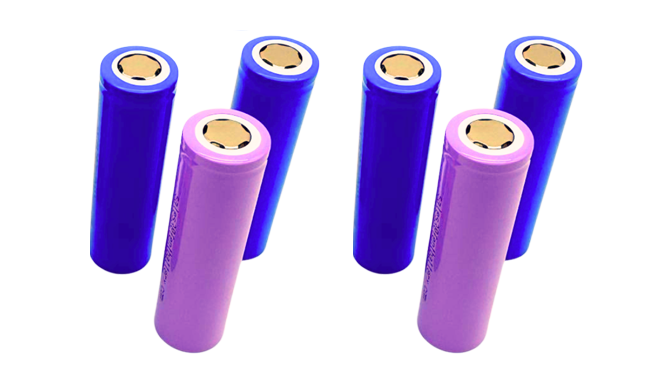
Pulping
Mix the positive or negative electrode active material in a certain proportion with specialized conductive agents, binders, and solvents, and prepare it into a slurry.
Raw material pretreatment: Positive electrode active material, conductive agent, binder are baked and dehydrated at atmospheric pressure, and solvents are dehydrated using dry molecular sieves or special material extraction facilities
Raw material mixing: a. Dissolution and heat treatment of binders; b. Ball milling of active substances and conductive agents
Dry powder dispersion: the process of wetting a solid with a binder liquid and extruding gas
All components in the positive electrode material can be wetted by the binder solution, so the dispersion of positive electrode powder is relatively easy
Dispersion method: Static method (long dispersion time, poor effect, but does not damage the original structure of the material)
Mixing method (short time, good effect, but may damage the material's own structure)
Mixing speed: The higher the speed, the faster the dispersion, but it causes significant damage to the material's own structure and equipment
Mixing temperature: suitable temperature, good fluidity of the slurry, easy dispersion, too hot slurry is prone to skin formation, too cold slurry reduces fluidity
Mixing concentration: The smaller the concentration, the faster the dispersion, but being too dilute can lead to material waste and increased precipitation of the slurry
Vacuum degree: High vacuum degree is conducive to the elimination of material gaps and surface gases, reducing the difficulty of liquid adsorption and making it easy to disperse evenly
Dilution: Adjust the slurry to a suitable concentration for easy coating
coating
Process function: Apply the slurry continuously and uniformly on the surface of the conveying current collector, dry it, and make positive and negative electrode sheets separately.
Principle: The coating roller rotates to drive the slurry, and the transfer amount of the slurry is adjusted by adjusting the gap between the scraper blades. The slurry is transferred to the substrate by the rotation of the back roller or coating roller. According to the process requirements, the thickness of the coating layer is controlled to meet the weight requirements. At the same time, the solvent in the slurry laid flat on the substrate is removed by drying and heating, so that the solid substance is well bonded to the substrate.
Technical route: Single layer coating, followed by back coating after drying, including continuous coating, fixed length slitting, and fixed length segmented coating. The coating process should adjust the gap between the coating machine head and tool according to the solid content and specific gravity of the positive and negative electrode slurry, and control the coating thickness
High quality polarizer: The polarizer surface is flat, smooth, evenly coated, with good adhesion, dry, non shedding, non missing, dust-free, scratch free, and bubble free.
Roll pressing
Process function: Compact the coated polarizer to achieve the appropriate density and thickness
Purpose: To make the active substance in close contact with the grid and current collector, reduce the distance of electron movement, decrease the thickness of the electrode, increase the loading capacity, improve the volume utilization rate of the battery, and increase the battery capacity
Principle: By adjusting the gap between the pressure rollers to regulate the pressure, the thickness and density of the compacted pole piece can be adjusted
Splitting
Process function: Cut the rolled polarizer roll into large pieces first, and then divide them into the required polarizer width according to the process requirements
Stacking process
The stacking process is a type of Li ion battery manufacturing process that involves cutting the positive and negative electrodes into small pieces and stacking them with an isolation film to form small battery cells. These small battery cells are then stacked and connected in parallel to form a large battery cell