18650 battery manufacturing process and key points!
18650 refers to the external specifications of the battery, where 18 represents a diameter of 18mm, 65 represents a length of 65mm, and 0 represents a cylindrical battery. It is the earliest, most mature, and stable lithium-ion battery model, with advantages such as high manufacturing automation, good battery consistency, high individual energy density, and good heat dissipation. Taking the 18650 cylindrical lithium-ion battery as an example, this article reveals the manufacturing process of lithium-ion batteries, analyzes the key control points of each process and their impact on the battery's electrical performance, and provides important references for the application of lithium-ion batteries.
1、 Lithium ion battery
1.1 Working principle of lithium-ion battery
Lithium ion batteries are mainly composed of a positive electrode, a negative electrode, a separator, and an electrolyte, relying on Li+to move between the positive and negative electrodes to work. During charging, Li+is detached from the positive electrode and embedded into the negative electrode through the electrolyte, resulting in the negative electrode being in a lithium rich state; When discharging, it is the opposite. Taking a lithium battery with lithium cobalt oxide as the positive electrode and graphite as the negative electrode as an example, the chemical reaction formula during charging is as follows:
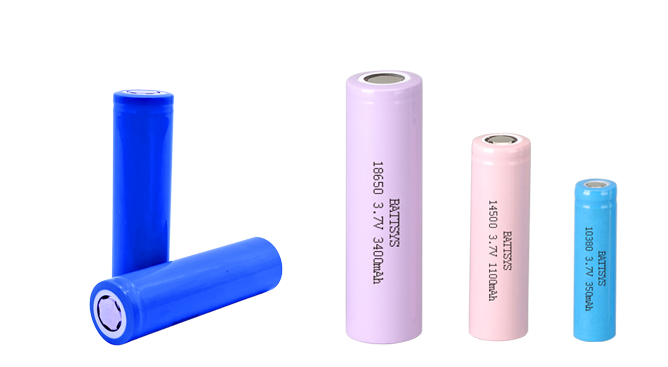
1.2 Lithium ion battery structure
Lithium ion batteries are mainly composed of four main materials: positive electrode, negative electrode, diaphragm, and electrolyte. Meanwhile, a complete 18650 cylindrical lithium-ion battery cell also includes auxiliary materials such as positive and negative electrode leads, upper and lower insulation sheets, cover plate, and outer steel shell, as shown in Figure 1.
2、 Manufacturing process and control points of lithium-ion batteries
The manufacturing process of lithium-ion batteries is complex and involves numerous steps. Any mistake in any step can affect the performance of lithium-ion batteries or cause safety issues. Therefore, only by strictly controlling each manufacturing process can qualified batteries with excellent performance and guaranteed safety be produced. Taking the 18650 cylindrical lithium-ion battery as an example, this article provides a detailed introduction to the manufacturing process of the battery and explains the key control points and their impacts for each manufacturing process. The manufacturing process is divided into three stages: the pre manufacturing stage, the post manufacturing stage, and the screening process, which are explained in sequence, as shown in Figure 2.
2.1 Pre production process and control points for lithium-ion battery manufacturing
The front-end process of battery manufacturing includes 10 steps: bonding, coating, rolling, slitting, slicing, winding, shell insertion, bottom welding, roller groove, and baking. The core of the front-end process is to make the powdered positive and negative electrode materials into a core roll.
The slurry mixing process refers to the uniform mixing of positive or negative electrode powder, conductive agent, and adhesive agent in a certain proportion to form a suspended slurry, and then coating a layer of uniform thickness on the surface of the current collector through a coating machine, which is the coating process. After coating is completed, the polarizer needs to be adjusted by a roller press to adjust the roller gap, winding position, tension, etc., and a test piece is used for pressure testing to ensure that the thickness of the test piece after pressure testing meets the process parameter requirements. Then use a slitting machine to cut into the width required for a single battery cell. Finally, weld the electrode ears on the wafer and apply insulation glue to cover the exposed current collector and electrode ears at the electrode ear position. At this point, the production of the positive and negative electrode pieces is completed.
The main process control point of the bonding process lies in the humidity control of the environment, because moisture is a key indicator that needs to be strictly controlled in the production process of lithium-ion batteries. Factors such as high environmental humidity and the use of water-based adhesives can lead to an increase in moisture content during the electrode preparation process; The slitting process needs to focus on controlling the size of burrs on the edge of the polarizer, and there should be no obvious material dropping, otherwise the polarizer may puncture the diaphragm due to material dropping or burrs being too large, causing a short circuit; The production process should prevent virtual soldering, off soldering, leakage soldering, or electrode chip dropping, as well as insulation glue off soldering or leakage soldering; The winding process is an important process for forming cylindrical lithium batteries. The strip shaped positive and negative electrode pieces and separator are wound into a cylindrical core by a winding machine. The key control point of this process is that the negative electrode piece must completely cover the positive electrode piece, and the separator must completely cover the negative electrode piece, which requires very high process accuracy. If the negative electrode is not fully wrapped around the positive electrode, lithium deposition may occur on the separator during the charging process. As the degree of lithium deposition increases, it can cause a short circuit between the positive and negative electrodes. Internal short circuit accidents caused by lithium dendrites are an important form of battery failure and may lead to accidents such as fire and explosion. If the diaphragm does not cover the negative electrode, it will directly cause contact between the positive and negative electrodes, resulting in a short circuit of the battery cell and causing serious safety accidents.
After the core is completed, it needs to be placed in the steel shell and connected to the negative electrode ear through bottom welding. At this point, the entire steel shell is the negative electrode of the battery, and the core inside the steel shell is fixed by the roller groove. The process of entering the shell and roller groove cannot damage the core, and the height of the roller groove must be strictly controlled. If it is too low, the core will be damaged; When it is too high, the core is prone to loosening. Finally, place the core that has been put into the shell in a baking oven until the moisture content of the core reaches the standard before proceeding to the next process. Baking is a crucial step to strictly control the moisture content of the core.
2.2 Post manufacturing process and control points of lithium-ion batteries
The post manufacturing process of batteries includes liquid injection, welding, sealing, cleaning, and film coating. Liquid injection refers to the process of injecting electrolyte into the baked core with qualified moisture requirements through a liquid injection machine. After the liquid injection is completed, the four main materials of the lithium battery are all applied to the core. The key to the liquid injection process is to precisely control the amount of liquid injection, humidity control, temperature control, and waterproofing, and to achieve the effect of good infiltration and penetration of electrolyte into the positive and negative electrode pieces. The amount of electrolyte directly affects the safety performance and capacity of the battery. If the injection volume is too high, the internal gas production of the battery will be large, and the safety valve of the cylindrical battery will often open prematurely; If the injection volume is too small, the battery capacity will be low and lithium will precipitate, which is more likely to cause thermal runaway or even explosion. Then weld the cover plate and the positive electrode ear together, and the entire cover plate becomes the positive electrode of the battery. The control point of welding is to prevent virtual welding, deviation welding, and poor appearance of the cap.
The next process is sealing, which seals the steel shell and cover plate, isolating the entire core from the external environment. The entire core is a sealed electrochemical system. The sealing process is the last crucial step in the entire battery cell manufacturing process, and the stability of its pressure forming technology determines whether the battery's sealing is intact and reliable. Completing the sealing process means that the manufacturing of a fully formed battery cell has been completed. The purpose of the cleaning process is to remove the residual electrolyte on the surface of the battery steel shell, prevent the electrolyte from corroding the steel shell, while the coating process is to ensure that the positive and negative terminals of the battery cell are separated, prevent external circuit short circuits, and give the battery a certain degree of aesthetics. These two processes also require screening for batteries with poor appearance.
2.3 Lithium ion battery screening process and control points
Due to differences in battery raw materials, production processes, and other performance factors such as battery capacity, voltage, and internal resistance, the performance of battery packs cannot reach the level of individual batteries, and their service life is much shorter than that of individual batteries, which affects the use of electric vehicles. The battery screening process includes activation, formation, aging, sorting, and capacity separation processes.
The activation process involves placing the battery cells in a constant temperature environment for a period of time after coating them, allowing the electrolyte to fully infiltrate the electrodes and separators to prevent lithium deposition due to uneven electrolyte infiltration. The activation process requires controlling the temperature and duration of the storage environment. The formation process is to charge the lithium ion battery for the first time. This process promotes the formation of a layer of "solid electrolyte interface facial mask" (SEI film) on the electrode surface. It refers to the interface facial mask formed during the first charge of the lithium ion battery due to the oxidation and reduction decomposition of the electrolyte and deposition on the surface of the electrode material. It has the characteristics of ion conduction and electronic insulation. Li+can be freely embedded and removed through this film. Because of the characteristics of its solid electrolyte, it is called "solid electrolyte interface facial mask".
SEI film is a guarantee condition for the long-term stable operation of lithium-ion batteries, which has a crucial impact on their capacity, rate, cycling, safety performance, etc. Choosing appropriate formation current, formation voltage, formation temperature, etc. plays a very important role in optimizing and improving battery performance. Therefore, this process is very important. In practical operation, it is necessary to prevent battery reverse connection, overcharging, and poor contact.
The aging process involves placing a battery cell in a constant temperature environment under a certain state of charge for a period of time, and filtering the data based on the voltage before and after testing to eliminate cells with large or abnormal voltage drops. When micro short circuits or severe side reactions occur inside a typical battery cell, the voltage drop of the cell will be significant, indicating poor performance and potential safety risks. Therefore, voltage drop is one of the important reference indicators for battery cell screening.
Due to the long aging time at room temperature, in order to shorten the production cycle, the vast majority of lithium-ion battery manufacturers adopt high-temperature or high charge state aging methods. The key points of process control need to closely monitor whether there are any abnormal situations during the storage process, and take timely action to ensure safety. As a general high-temperature aging room is a closed space, it is not easy to be detected in the initial stage. Once a fire occurs, the consequences are unimaginable.
The sorting process is to select cells with different internal resistance levels based on the AC internal resistance of the cells, eliminate cells with abnormal internal resistance, and easily select suitable cells for series or parallel combination. Therefore, internal resistance is also an important reference indicator for cell screening.
The capacity division process involves selecting cells according to different capacity levels after measuring their capacity, and removing cells with unqualified capacity. Due to the significant relationship between capacity and temperature, the more accurate the environmental temperature control during capacity division, the closer the capacity is to the true value, and the more accurate the level allocation. Therefore, temperature control is the key to capacity division control. The shipped battery cells must be qualified cells that have undergone voltage drop, internal resistance, and capacity screening.