What are the factors affecting the discharge capacity of 18650 lithium battery PACK?
Lithium ion batteries have the advantages of large capacity, high specific energy, good cycle life, and no memory effect, and have developed rapidly. Capacity, as its most critical performance indicator, has also attracted the attention of researchers. Correspondingly, lithium battery PACKs are constantly developing towards high capacity, fast charging, long lifespan, and high safety, which also puts forward new requirements for the manufacturing process technology.
Lithium ion battery PACK mainly involves conducting electrical performance tests on battery cells after screening, grouping, packaging, and assembly to determine whether the capacity and pressure difference of the products are qualified.
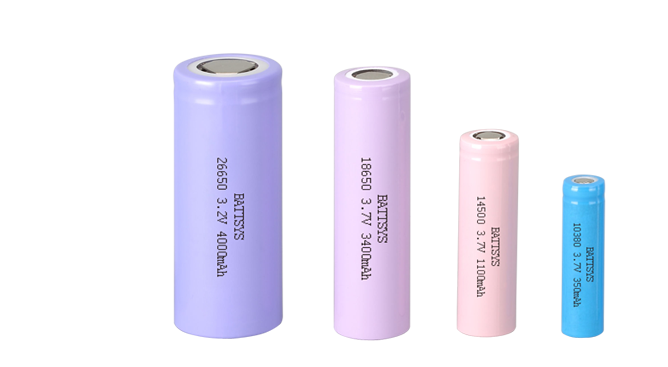
The consistency between battery series and parallel units needs to be specially considered in battery pack. Only with good consistency in capacity, state of charge, internal resistance, self discharge, etc. can the capacity of the battery pack be fully utilized and released. Poor consistency can seriously affect the overall performance of the battery pack, and even cause overcharging or overdischarging, resulting in safety hazards. A good composition scheme is an effective way to improve monomer consistency.
Lithium ion batteries are constrained by environmental temperature, and high or low temperatures can affect battery capacity. The cycle life of batteries working under high temperature conditions for a long time may be affected, and if the temperature is too low, the capacity may not be fully utilized.
1、 Consistency in grouping
Good combination can not only improve the utilization rate of battery cells, but also control the consistency of individual cells, which is the basis for achieving good discharge capacity and cycle stability in battery pack discharge. The dispersion of AC impedance of poorly matched battery cells will intensify, thereby weakening the cycling performance and available capacity of the battery pack.
Xu Mengfei proposed a method for battery assembly based on the characteristic vectors of batteries. This feature vector reflects the degree of similarity between the charging and discharging voltage data of a single battery and the charging and discharging data of a standard battery. The closer the charging and discharging curve of the battery is to the standard curve, the higher its similarity, and the closer the correlation coefficient is to 1. This grouping method mainly relies on the correlation coefficient of individual voltage, combined with other parameters for grouping, which can achieve a relatively good grouping effect. The difficulty of this method lies in the need to provide standard battery feature vectors. Due to the limitations of production level, there must be differences between each batch of batteries produced, making it very difficult to obtain a set of feature vectors that are suitable for each batch of batteries.
Zhang Jianfeng et al. used quantitative analysis to analyze the differential evaluation methods between individual batteries. Firstly, mathematical methods are used to extract the key points that affect battery performance, and then mathematical abstraction is carried out to achieve comprehensive evaluation and comparison of battery performance. The qualitative analysis of battery performance is transformed into quantitative analysis, proposing a simple and practical method for the optimal combination of comprehensive performance of battery packs. A comprehensive performance evaluation system based on battery screening and grouping has been proposed, which combines subjective Delphi scoring with objective grey correlation degree calculation to establish a multi parameter grey correlation model for batteries. This overcomes the one sidedness of using a single indicator as the evaluation standard and achieves performance evaluation of power type power batteries. The correlation degree obtained from the evaluation results provides a reliable theoretical basis for the later screening and grouping of batteries.
The dynamic characteristic grouping method mainly implements the grouping function based on the charging and discharging curve of the battery. The specific implementation steps are to first extract the feature points on the curve, form a feature vector, and use the distance between the feature vectors of each curve as the grouping index. By selecting an appropriate algorithm, the curve classification is achieved, and then the battery grouping process is completed. This grouping method takes into account the performance changes of the battery during operation. On this basis, selecting other suitable parameters for battery assembly can select batteries with consistent performance.
2、 Charging method
The appropriate charging system has a significant impact on the discharge capacity of batteries. If the charging depth is shallow, the discharge capacity will correspondingly decrease. If overcharged, it will affect the chemical active substances of the battery, causing irreversible damage and reducing the capacity and lifespan of the battery. Therefore, it is necessary to choose an appropriate charging rate, upper limit voltage, and constant voltage cutoff current to ensure optimal charging efficiency and safety stability while achieving charging capacity.
The consistency of SOC among individual cells largely determines the discharge capacity of the battery pack, and balanced charging provides the possibility to achieve similar initial SOC platforms for individual cell discharge, which can improve discharge capacity and efficiency (discharge capacity/group capacity). The balancing method in charging refers to the balancing of power batteries during the charging process, usually starting to balance when the individual voltage of the battery pack reaches or exceeds the set voltage, by reducing the charging current to prevent overcharging.
Qi Huaming proposed a balanced charging control strategy that can achieve fast charging of the battery pack and eliminate the impact of inconsistent individual cells on the cycle life of the battery pack, based on the different states of individual cells in the battery pack. The strategy involves using a battery pack balanced charging control circuit model and fine-tuning the charging current of individual cells through the balancing circuit. Specifically, through switch signals, the overall energy of the
lithium-ion battery pack is replenished to individual cells, or the energy of individual cells is converted to the overall battery pack. During the charging process of the battery pack, the balancing module starts working by detecting the voltage values of each individual cell. When the voltage of each individual cell reaches a certain value, the balancing module begins to operate. Diverting the charging current in a single battery to reduce the charging voltage, the separated current is converted by a module to feedback energy back to the charging bus, achieving the goal of balance.
Zhang Zhi proposed a variable rate charging balance solution, which aims to provide additional energy supply only to low energy individual batteries, avoiding the process of extracting energy from high energy individual batteries. This greatly simplifies the topology of the balance circuit. By using different charging rates to charge individual batteries of different energy states, a good balance effect can be achieved.
3、 Discharge rate
The discharge rate is a crucial indicator for power type power batteries. The high rate discharge of batteries is a test for positive and negative electrode materials and electrolytes. For the positive electrode material lithium iron phosphate, its structure is stable, the strain during charge and discharge is small, and it has the basic conditions for high current discharge. However, the disadvantage is that the conductivity of lithium iron phosphate is poor. The diffusion rate of lithium ions in the electrolyte is the main factor affecting the discharge rate of the battery, and the diffusion of ions inside the battery is closely related to the structure of the battery and the concentration of the electrolyte.
Therefore, different discharge rates lead to different discharge times and voltage platforms of the battery, resulting in different discharge capacities, which is particularly evident for parallel battery packs. Therefore, it is necessary to choose an appropriate discharge rate. The relationship between discharge capacity and discharge rate (current) can be described by the Peukert equation:
In the formula: I is the discharge current; N is the Peukert constant, which is related to the structure of the battery and ranges from 1.15 to 1.42; K is a constant that is related to the amount of active substance in the battery.
The available capacity of the battery decreases with the increase of discharge current.
Jiang Cuina et al. studied the effect of discharge rate on the discharge capacity of lithium iron phosphate battery cells. A group of cells with good initial consistency of the same model were charged at 1C current to 3.8V, and then discharged at discharge rates of 0.1, 0.2, 0.5, 1, 2, and 3C to 2.5V. The relationship curve between voltage and discharge capacity was recorded, as shown in Figure 1. The experimental results show that the capacity released by 1 and 2C is 97.8% and 96.5% of the capacity released by C/3, respectively, and the energy released is 97.2% and 94.3% of the energy released by C/3, respectively. It can be seen that with the increase of discharge current, the capacity and energy released by lithium-ion batteries decrease significantly.
accadc1d21b7364368c2f318b087a506.png
When discharging lithium-ion batteries, the national standard 1C is generally used, and the maximum discharge current is usually limited to 2-3C. When discharging with high current, there will be a significant temperature rise and energy loss. Therefore, it is necessary to monitor the temperature of the battery pack in real time to prevent excessive temperature from causing damage to the battery and reducing its service life.
4、 Temperature conditions
Temperature mainly affects the activity of electrode materials and electrolyte performance inside the battery. Both high and low temperatures have a significant impact on the capacity of batteries.